Continuous improvement is a principle designed for businesses, teams and individuals. The principles help you escalate your habits towards a good direction and hence help with every operation you participate in. Not a paradigm shift or invention, but slow and steady progress is the most innovative. It helps apply change easier, as well as giving the reins to the organization rather than having to respond to external forces.
Continuous improvement is led by the following Kaizen principles
Feedback: Feedback is crucial and one of the core of Kaizen's principles. In a continuous improvement environment, without feedback you won’t be able to go very far. Strong feedback helps in assessing our position and figure out the improvement areas.
Efficiency: Continuous improvement brings about efficiency in the overall processes. Things don’t stay in line when It's overall purposes is to identify, cut down and eliminate blockers or retarded processes.
Evolution: As per kaizen, the processes need to continuously evolve and get better with help from the necessary stakeholders. The key of evolution of processes is continuous improvement need to evolve at a natural pace and they need to be The emphasis of continuous improvement is reflected in evolution.
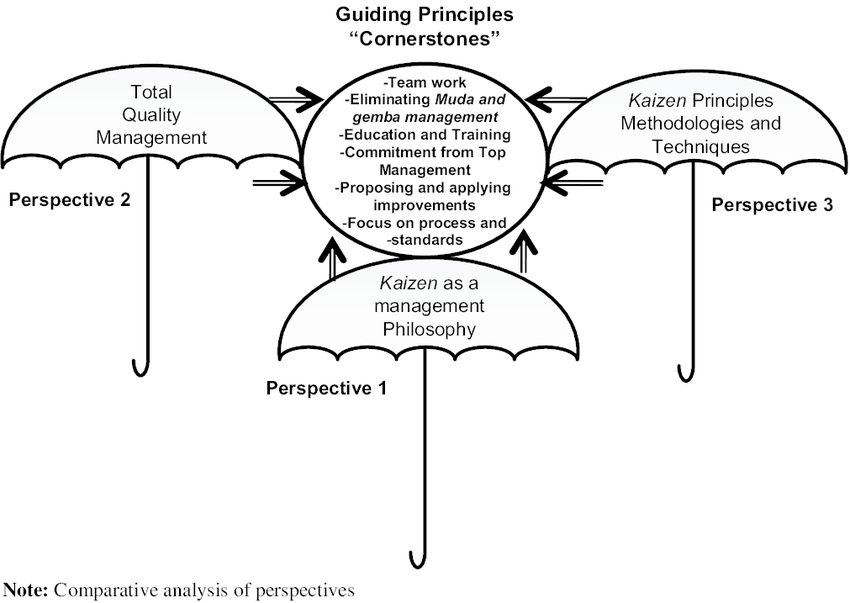
The team should chip in ideas
The management doesn’t need to be involved in every idea or thought, the ideas should be coming from the team instead. Since the team works and knows which process or thing needs to get better and which areas require better approach. The team should feel free to bring in thought through ideas which have the potential to revamp some or the other process and can bring about impactful change in the process.
Gradual change isn’t heavy on the finances
Dramatic changes can be very costly for the organization and they may change a lot of things as well. But changes if done gradually can prove to be very economical for any given business. They are held under some budget constraints and they take place under strict guidelines and surveillance by the management and the team. Hence, small changes are not heavy on the finances.
Workers Take Ownership and Accountability
A lot can be achieved by giving employees total ownership or maybe under jurisdiction in some instances where the management is totally risk averse. This way employees stay more invested and interested in getting things done and making sure everyone is being solely accountable for their respective roles, motivation also comes when people are made feel responsible and self accountable.
Improvements Can Be Measured and Repeated
Once a change is made, it’s not left alone but monitored and measured, so determinations can be made as to its effectiveness. Therefore, if that change does work, it can be repeated or applied to other aspects of the organization.
The importance of gaining feedback in a continuous environment
Feedback plays a crucial role in defining the course of action and making sure that you have a direction to head in. You can imagine a situation where feedback wasn’t a part of your work, you wouldn’t have been able to improve or make changes Imagine if feedback was not a part of whatever you do, you would find it very tough to grow in any environment if you are not aware of your improvement areas.
Why to imbibe continuous improvement?
Depending on the size of your company and the degree to which is implemented, you may see various results. Below are some common benefits that have been gained as a result:
- Improved product quality
- Increased efficiency and productivity
- Decreased cost
- Reduced waste
- Employee satisfaction and teamwork
- Customer satisfaction
As you can surmise from the list above, the advantages of continuous improvement can be exponential. In addition to financial benefits, employees who work on improving the company tend to feel more personally accomplished--leading them to stay longer at the organization and producing more impactful results.
How to build a culture for continuous improvement ?
If you, the manager, personally lead every single process improvement initiative, you’re not likely to make any lasting change. More often than not, it’s the employee that knows how to work with the process best, not their supervisor. You want to empower them with the tools and ability to carry out process improvement when need be.
The key to establishing a culture of continuous process improvement is to make it a part of company culture. It should start top-down from the organization – the C-suite should encourage the management to make suggestions on process improvement. This, in turn, will trickle down from the management to shop-floor employees.
- Everyone’s suggestions and considered and evaluated. The employees are made aware of the reasoning for accepting certain suggestions and rejecting others.
- To ensure that the employees do a better job in the long-term, you hold training on process analysis.
- Offer different incentives for employees to help with process improvement. This can be in the form of bonus pay, physical gifts, etc.
The remainder
Inculcating continuous improvement in any process is going to be a collaborative process which involves people from different departments to come together and align the bottlenecks in their processes. Sometimes it can be very exhausting to bringing about change in the organisation as a whole but it is all worth it when you experience staggering change across many functions.
Subscribe
Related Blogs
Exploring Drupal's Single Directory Components: A Game-Changer for Developers
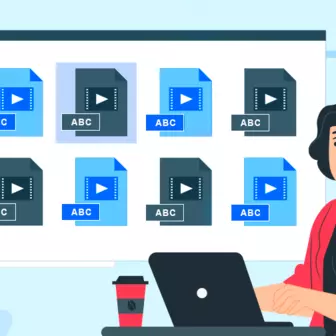
Web development thrives on efficiency and organisation, and Drupal, our favourite CMS, is here to amp that up with its…
7 Quick Steps to Create API Documentation Using Postman
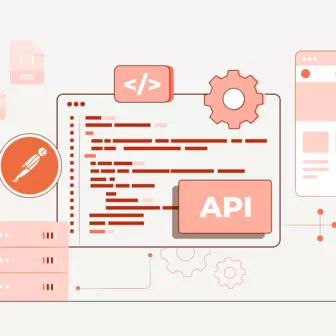
If you work with API , you are likely already familiar with Postman, the beloved REST Client trusted by countless…
What is Product Engineering Life Cycle?
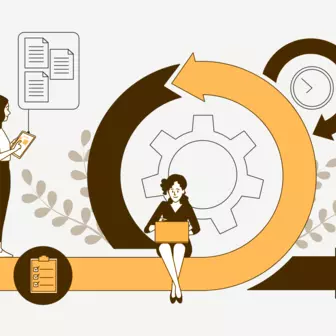
Imagine constructing a house without a blueprint or a set of plans. It will be challenging to estimate the cost and labor…